Metallurgy:
(Prehistoric Evidence of...)
A Chronology of Prehistoric Metallurgy: |
Metallurgy in Europe.
The Earliest Copper
Mining
Europe: (Vinca Culture, c. 5,000 BC).
The early Neolithic
mine of Rudna Glava near Majdanpek is an
example of the oldest known technology of Vinca copper working. The developed
skills of the Rudna Glava miners are indicated by the ore-emptied shafts no less than 20m deep.
Stone mallets, made from river stones
of volcanic rock, gives evidence of the higher
specialization of primitive tools for different and
various productive purposes. As for the chopping of the pieces
different types of wedges were used, while the tools made from
deer horns were used for gathering the ore already chopped.
When an ore vein was
discovered, the access platform was built round its flooding
canal. Afterwards the hard ore mass was broken into pieces by
circular hits with stone mallets, hanged either on a rope or leather
belt. In the depths, the technique of heating then cooling
suddenly was
used. Large ceramic dishes were used for
pouring the water over the hot ore blocks. Cracked blocks were
further smashed and broken into pieces.
The ore obtained was
taken to the surface in bags, and it was distributed to
the settlements near by. Further metallurgic processes are
considered to be a part of technological circle of handworks in
that early period of metal usage.
-
(Full Article:
http://www.muzej-mpek.org.yu/e_rglava.htm)
Article:
(Bulgaria
- c. 3,000 BC) - Thousands of uniformly 'pressed' gold 'beads'
were discovered in a Thracian horde in the Bulgarian 'Valley of the Kings'.
The beads, which are only millimetres in diameter, have the appearance of
minute 'washers', which show evidence of 'pressing' on both sides. The
amount discovered, and their uniformity, have led to the suggestion that
they were mass-manufactured, or machine made.
(Ref: UK Ch4 News 31.8.2005)
|
The first Metalworkers in
the UK - (4,000 BC - 2,000 BC) The New Scientist.
The following article questions the origin of the raw materials and science
used for the 'Copper-age' and 'Bronze-age' in ancient Britain.
Copper-arsenic alloys were used throughout mainland Europe and the Middle
East during the 'Copper Age', the slow transition from the late Neolithic to
the Bronze Age between about 4000 and 2500 BC. These prehistoric 'arsenical
coppers' span the period between the first smelting of copper and the
development of bronze, which is an alloy of copper and tin.
'Until recently most
archaeologists assumed that arsenical coppers were the first
intentionally produced alloys. Various arguments were put forward in
favour of this idea, stressing the advantages of arsenical copper
over pure copper as a material for making tools and weapons. The
arguments were based on some well-known facts about arsenic. For
example, it could act as a deoxidant in casting, preventing the
metal becoming too brittle, and it increased the hardness of edges
formed on tools and weapons by hammering.
There are various opinions
about which methods were used to introduce the arsenic, but by the
1970s most researchers believed that the arsenic was there because
Bronze Age metalworkers had selected copper ores that were naturally
rich in the element. Copper ore deposits are usually laid down in
rock fissures or veins as primary copper sulphide minerals. Exposed
areas of such deposits are converted to secondary minerals such as
oxides and carbonates. Within some primary copper deposits are the 'fahlerz'
ores, which contain arsenic and the metal antimony. The metalworkers
had apparently discovered that these ores yielded a superior
produc't.
When archaeologists
put metal artefacts in chronological order, they have always assumed
that as metals technology evolved, simple designs and materials would
gradually be replaced by more sophisticated and specialised ones.
Comparisons between such metalwork typologies for various parts of
Europe supported the diffusion hypothesis. They revealed that the pace
of metallurgical development varied greatly. Metals appeared later
in the archaeological record of north-western Europe than in the south
and east, for instance, and southern metal artefacts appeared to be
more advanced than northern European forms of the same age.
'While some archaeologists were
classifying metal artefacts by their physical appearance others
began to analyse their composition, especially after spectrographic
methods became widely available in the 1930s. This approach,
pioneered by the German chemists Helmut Witter and Wilhelm Otto and
the Austrian scientist Richard Pittioni, culminated in a massive
programme, based in Stuttgart, which was responsible for more than
16 000 analyses of Early Bronze Age metalwork by the mid-1970s'.
By then, metalwork
typologies for Britain were already well developed as were ideas,
partly based on them, about the origins of British metallurgy. The
appearance of metals in the archaeological record of the British Isles
was associated with other changes, particularly a shift in burial
practices and the appearance in graves of a new form of pottery,
shaped like a small cup or beaker. Archaeologists had found evidence
for similar changes in central Europe and Iberia at the beginning of
the Bronze Age, and it seemed likely that Britain was invaded and
settled by a new population from elsewhere in Europe, possibly the
Rhineland. It was these 'Beaker Culture' settlers who were thought
to have brought a knowledge of metals to Britain. Not only that,
but axes, by far the most common Early Bronze Age artefact, were
unevenly distributed across the British Isles: there are heavy
concentrations in Ireland, most of the earliest forms in the
south-western region of Munster. It seemed clear that metallurgy was
introduced to Britain via Ireland.
'Confirmation
that the earliest Irish Bronze Age tools were high in arsenic
was supported by findings of the same impurity pattern in the few
artefacts of this period found elsewhere in the British Isles. This
led him to the proposition that an Irish metal industry had existed,
supplying England, Scotland and Wales with copper during the
earliest Bronze Age, based on the exploitation of
fahlerz ores from
southwest Ireland. The high levels of arsenic in early bronzes in
Ireland and the rest of the British Isles indicated that the early
Irish industry had continued well into the Early Bronze Age. Only
later did centres of production develop outside Ireland; these made
more developed forms of flat axe in which the metal had different
impurity patterns, including relatively high levels of nickel'.
Although the significance of arsenical copper in
the earliest part of the Bronze Age is still disputed, it does seem
that arsenical copper was not intentionally produced in order to make
better tools. On the contrary, there is now a large body of evidence,
including the compositions of copper artefacts, to suggest that the
processes used to smelt the metal were very primitive, and may have
restricted early metalworkers to the use of particular types of ore
deposit.
Clearly, the technology was not
well developed and there is no reason why it should have been
introduced as a result of population movement. The fact that
accessible deposits of suitable minerals are far more widespread in
other parts of the British Isles than they are in Ireland makes one
suspicious of any suggestion that Britain's earliest metal
production was based exclusively there.
The article ends with the
following words...again raising more questions than answers...
'Of course, we can never be sure of
the sequence of events more than four thousand years ago which led to
the production of the first metal artefact in the British Isles. But I
am sure that Beaker Culture metallurgists from the Rhineland never
stalked the Munster (Irish) countryside in search of fahlerz
ores to make it'.
(Ref:
http://www.newscientist.com/article/)
Metallurgy in the Middle-east.
Having already mentioned that metals
appeared later in the archaeological record of north-western Europe than in the south and
east, and that southern metal artefacts appeared to be more advanced
than northern European forms of the same age, we can now support this with
earlier discoveries from the middle-east, as the following examples
demonstrate. It is a reasonable conclusion that European metallurgy had a
Middle-eastern origin...
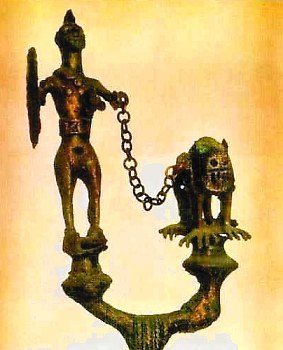 Metsamor (Medzamor),
Armenia
-
Metsamor has revealed foundries that were processing
metal as far back as 5,000 BC. The site contains the oldest large-scale
metallurgical factory in the world (2,500 BC). Discovered by Dr Koriun Megatchian, in Soviet Armenia (20Km from Ararat). It contained over 200 furnaces,
producing an assortment of vases, knives, spearheads, rings, bracelets, etc.
The Metsamor craftsmen wore mouth-filters and gloves while they laboured and
fashioned their wares of copper, lead, zinc, iron, gold, tin, manganese and
fourteen kinds of bronze. The smelters also produced an assortment of metal
paints, ceramics and glass. But the most out-of-place discovery was several
pairs of tweezers made of steel, taken from layers dating back before the
first millennium BC. The steel was later found to be of exceptionally high
grade, and the discovery was verified by scientific organizations in the
Soviet Union, the United States, Britain, France and Germany. (9).
(Click here for more about Metsamor)
Metallurgy in Africa.
Egypt: The Great pyramid of Giza: Iron plate found in
'star-passage'. (See below)
Tanzania
- 1,500 AD - The discovery
of steel-smelting ovens (producing carbon steel), achieving temperatures of
1,800 centigrade (3)
The South African spheres
- 'The Klerksdorp Spheres':
Quote from (1) - 'Over the past several decades, South African miners
have found hundreds of metallic
spheres, at least one of which has three parallel grooves running around its
equator. The spheres are of two types - "one of solid bluish metal with
white flecks, and another which is a hollow ball filled with a white spongy
centre" (Jimison, 1982). The sphere
in the photos (below), was found in a Precambrian mineral deposit, making it
an unlikely 4,500 Million years years old. Some of the spheres
can be seen in the Museum at Klerksdorp, South Africa. (3)
At least 200 have been found, and extracted out of deep
rock at the Wonderstone Silver Mine in South Africa, averaging 1-4 inches in
diam. and composed of a nickel-steel alloy that doesn't occur naturally.
Some have a thin shell about a quarter inch thick, when broken open are
filled with a strange spongy material that disintegrates into dust upon
contact with air.
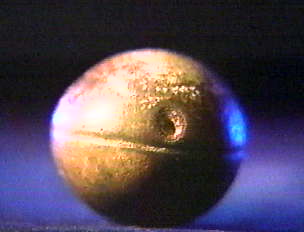
(More about the 'Klerksdorp Spheres') |
Metallurgy in the America's.
Peru - Pre Inca
ornaments and other objects made of Platinum have been discovered. (The
Melting Point of platinum is 1,755 degrees Celcius).
(9)
( More about ancient Peru)
Metallurgy in Asia.
China
- An aluminium belt fastener with open-work
ornamentation was found in the grave of General Chou Chu of the Chin
dynasty, who lived from 256-316 AD. The fastener was examined by the
Institute of Applied Physics of the Chinese academy of Sciences and by the
Dubai Polytechnic. The process of extracting aluminium from Bauxite today
involves the use of a 'Reverbier' oven, refraction chamber and regenerator,
as well as electrolysis and temperatures exceeding 950�
Celcius. (9)
Meteoric Iron - Also recorded from China are 'two
puzzling ancient iron axes' dated c. 1000 B.C. - almost half a millennium
before iron working began in China - which were finally identified as
meteoric nickel-iron. In ancient Mexico, Indian ploughshares were made of
meteoric iron, and the Greenland Eskimos had a long tradition of using
meteoric iron for harpoons.
(2)
Metal in the Great Pyramid: |
There were several metal items found in the Great
pyramid of Ghiza:
The
Iron Plate
- On Friday, 26 May 1837, after a few days of blasting and clearing, J.
R. Hill (working for Vyse), discovered a flat iron plate about 26 cm
(10.2") long, 8.6 cm (3.4") wide, with a thickness ranging from .4 cm
(.2") to nearly zero, from a joint in the masonry at the point where the
southern airshaft from the King's chamber exits the pyramid. Engineers
agree that this plate was left in the joint during the building of the
pyramid and could not have been inserted afterwards. Colonel Vyse sent
the plate to the British Museum.
Hill affirmed that his find was legitimate:
This is to certify,
that the piece of iron found by me near the mouth of the air-passage,
in the southern side of the Great Pyramid at Gizeh, on Friday, May
26th, was taken out by me from an inner joint, after having removed by
blasting the two outer tiers of the stones of the present surface of
the Pyramid; and that no joint or opening of any sort was connected
with the above-mentioned joint, by which the iron could have been
placed in it after the original building of the Pyramid.
I also shewed the exact point to Mr. Perring, on
Saturday, June 24th.
(Vyse, Pyramids of Gizeh,
I, p. 276)
The plate was examined by the famous Sir Flinders Petrie
in 1881. He felt it was genuine and stated that...
"no reasonable doubt can therefore exist about
its being a really genuine piece".
Extract from Petrie -
That sheet iron was employed we know, from the
fragment found by Howard Vyse in the masonry of the south air channel;
and though some doubt has been thrown on the piece, merely from its
rarity, yet the vouchers for it are very precise; and it has a cast of
a nummulite on the rust of it, proving it to have been buried for ages
beside a block of nummulitic limestone, and therefore to be certainly
ancient. No reasonable doubt can therefore exist about its being
really a genuine piece used by the Pyramid masons; and probably such
pieces were required to prevent crowbars biting into the stones, and
to ease the action of the rollers.
H.R. Hall wrote of
the plate in "Note on the Early Use of Iron in Egypt" (Man 3, 1903):
Now that
Professor Petrie has discovered iron in deposits of VIth Dynasty date
at
Abydos, the contentions of those Egyptologists who have
always maintained that iron was known to the Egyptians from the
earliest times must be acknowledged to be correct. The fact that iron
was known to, and used by, the Egyptians over 2,000 years before it
came into use in Europe is very remarkable, and it is hard to square
with current theories, but it is a fact. Professor Petrie's find is a
lump of worked (?) iron, perhaps a wedge, which is rusted on to a bent
piece of copper...
This is the third find of iron which can be attributed
to the Old Kingdom. In 1837 a fragment of wrought-iron was discovered
in an inner joint of the stone blocks in one of the air-passages which
pass upwards from the interior of the Great Pyramid to the outer air [Vyse,
Pyramids of Gizeh, I., 276; Beck, Geschichte des Eisens, I., 85]. This
is now in the British Museum, Egyptian Department, No. 2433 (3rd
Egyptian Room, Case K, 29). In 1882 Professor Maspero found iron in
the pyramid of a Vth Dynasty king at Ab�s�r. Professor Petrie has now
found iron in a VIth Dynasty deposit at Abydos... The presumption now
is that the iron fragments from Ab�s�r and from the Great Pyramid are
of a Vth and IVth Dynasty date respectively. The G�za fragment will be
about 150 years older than the piece from Abydos. (pp. 147-49)
Tests were actually made in the British Museum
Laboratory, and since it seems desirable that the matter should be
cleared up, Dr. J.H. Plenderleith reported the following:
The Pyramid piece was found to consist 'of a thin
film of metallic iron with a more or less thick coating of its
oxides.' Samples were examined and 'no nickel could be detected.' This
was in November 1926; in April 1932 it was examined again, and the
results 'completely bear out the findings of the previous analytical
report as regards to the absence of nickel;' separate tests were
applied to the exterior scale and to the surface of the metallic iron
itself, and nowhere could nickel be detected. As Dr. Plenderleith was
advised that 'all known meteoric iron contains some nickel, about 4-30
per cent,' he considered it 'unnecessary to go any further in the
matter of chemical investigation.' The account of the result quoted
from Man (cf. also Dr. Rickard's Man and Metals 1932, II, 834) seems
therefore to have mislead Mr Wainwright.
The pyramid piece contains no detectable 'traces' of nickel.
In 1989, an analysis of the iron plate was made by El
Sayed El Gayar and M.P. Jones, published in their article "Metallurgical
investigation of an iron plate found in 1837 in the Great Pyramid at
Gizeh, Egypt" (Journal of Historical Metallurgy Society, Vol. 23
No. 2, 1989, pp. 75-83). El Gayar and Jones, using a hacksaw, carefully
cut off a small corner of the plate for analysis. This fragment was
triangular in shape with an area of 1 cm and a weight of 1.7g. After
again determining that the iron contained "only a trace of nickel",
thus confirming a terrestrial origin (p. 81), the authors found that the
plate consists of numerous laminates of wrought iron and that these
laminates have been inexpertly welded together by hammering. The various
layers differ from each other in their grain sizes, carbon contents, the
nature of their non-metallic inclusions, and in their thicknesses...
None of the iron layers contains siliceous, slaggy inclusions.
Furthermore, none of the other phases within the iron laminates shows
any metallic copper globules, nor do they show more than small
traces of the element copper. These features suggest that the
Gizeh iron plate had not been produced as a by-product of copper
smelting operations. The outer layers of the iron have been badly
corroded and now exist as complex banded iron oxides. Small, but
significant, proportions of gold were found in one of the oxidised
layers and it is thought possible that the plate may, originally, have
been gold-plated.
Drs. Jones and Gayer concluded the following: "It is
concluded, on the basis of the present investigation, that the iron
plate is very ancient. Furthermore, the metallurgical evidence supports
the archaeological evidence which suggests that the plate was
incorporated within the pyramid at the time that structure was being
built".
A more recent analysis of the plate, however, has cast
doubt on the findings and conclusions of the study by El Gayar and
Jones. In their article "Gizeh Iron Revisited" (Journal of the
Historical Metallurgy Society, Vol. 27 No. 2, 1993, pp. 57-59), Paul
Craddock and Janet Lang of the British Museum reported that they were at
first unable to obtain the section cut by El Gayar and Jones,
consequently the initial study was confined to the larger portion of the
plate. A new section was cut adjacent to the original section, and it
was examined under a scanning electron microscope both at the British
Museum and independently at the Ancient Monuments Laboratory, English
Heritage (the work was carried out there by Dr. G. McDonnell). It was
also analyzed by x-ray fluorescence. Surprisingly, no gold was detected
in the metal or in the corrosion. Craddock and Lang further wrote:
Since the last
report the original section has been returned to the Museum and we
have been able to carry out a thorough investigation. Once again we
must report that despite extensive searches no trace of gold could be
detected, and it is our firm opinion that the original report of gold
is incorrect.
The authors agreed with El Gayar and Jones regarding the
structure of the iron plate, but they did not agree on the
interpretation. They conclude the following - 'The structure of the
plate is consistent with iron-making in the post-medieval Islamic era'.
Comment - The plate has been determined of terrestrial
origin. It was declared of ancient origin because of the numulite
imprints in it. This was a specific observation, as was the
determination that it could not have fallen in at a later date. Other
contemporary findings of iron support the idea that this could at least
be genuine.
The royal funerary Pyramid Text �907 reads: The doors of
bA-kA [an unknown region of the sky] which is in the firmament are
opened for me, the doors of iron which are in the starry sky are thrown
open for me, and I go through them ...
And finally, this extract from Miracle in Stone.
(It does seem strange that none of the learned professors above ever
noticed it):
'The
Siniatic Mountains and hills are known to be full of
iron of the most excellent kind. A Mr. Hartland some years ago,
established himself in that region for mining purposes, and there,
near Surabit-el-Khadem ,and not far from Wady Meghara, he found, not
traces merely, but colossal remains, of iron works and furnaces,
belonging to the earliest kings of ancient Egypt, and on a scale so
vast as to be testified to by almost mountainous heaps of genuine iron
slag and veritable iron furnace refuse (see proceedings Soc. Antiq.,
Vol V, 2d series, June 1873). Nay. What is
more remarkable, here also, is a tablet containing the cartouches of
Shufu (Cheops) and Nem-Shufu, the same as the quarry-marks discovered
by Colonel Howard Vyse on the hidden stones in the Great Pyramid!
These records are engraved in a soffit in the face of the natural
rock, where they directly overlook the scene of the furnaces. They
begin with the name of Soris, the immediate predecessor to Cheops,
under whom the Egyptians seem to have been put through an
apprenticeship of working in iron. One of Egypt's ancient kings also
appears on the monuments with a name which means "A lover of Iron".'
Apart from the obvious implications of an Iron works with
the cartouches of fourth dynasty kings on it, it is interesting that the
name 'Soris' is mentioned, as this seems to confirm Manetho's
chronology. It also implies that Iron was understood and forged
before the pyramid was built. Just how big is this mine and where is
the Iron?
There
is also some Copper in the Great pyramid.
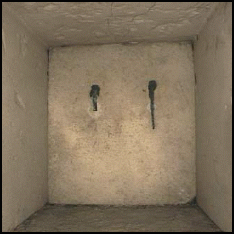
Queens Northern Shaft.
Queens Southern Shaft.
Both the shafts leading from the queens chamber have
copper 'handles' at their ends. Their significance is yet to be
determined but their presence in such a hidden and inaccessible internal
part of the structure is an absolute proof that metal-working was
present at the time of the 4th dynasty.
(More about the Great pyramid)
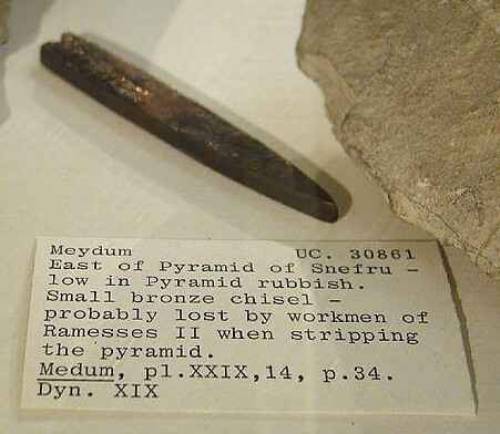
Bronze Chisel from the Cairo Museum. c. 2,000 BC.
The metallic �tubes� from Saint-Jean
de Livet (France)
In 1968, Y Druet and
H Salfati claimed to have discovered a number of semi-ovoid metallic
tubes they believed to be artificial in Cretaceous (Aptian) chalk at a
quarry in St-Jean de Livet (France), which they announced in a letter to
the editors of Plan�te, a French magazine devoted to
unsolved mysteries. The tubes were shaped identically, but their sizes
varied between 30 and 90 mm in length, and 10 and 40 mm in width.
According to the authors of the letter (dated 30 September 1968), the
objects were currently being studied by the Geomorphology Laboratory of
the Universit� de Caen, but nothing further seems to be known about
them.
|
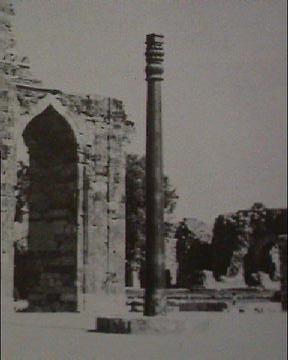
India - The Iron Pillar of Delhi (Photo, left), in the courtyard of
Qutub Minar in Delhi. It is
a column of Cast Iron weighing approx. 6 tons and standing 23ft 8 inches
high, with a diameter of 16inches. The column had stood in the temple of
Mutra, capped with 'Garuda', an image of a bird incarnation of the God
Vishnu. Muslim invaders later destroyed the 'Garuda' and tore the column
from its original setting, re-erecting it in Delhi in the 11th century AD.
It bears an inscription of an epitaph to King Chandragupta II, who died in
413AD. The bar shows some weathering, but unusually little rust.
(9)
(Prehistoric India)
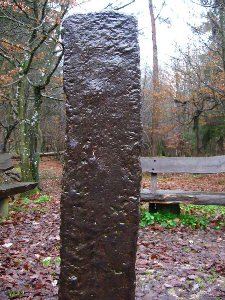
Der Eiserne Mann
The 'Iron Man
of Kottenforst', Bonn
The pillar has the appearance of a squared metal bar, about 1.47 m above ground and approximately 2.7 m below
ground. It was first mentioned in a document in 1625 as part of the border
line between Alfter and Heimerzheim along the Roman aqueduct .
Associated
with the Iron man are an ancient stone walkway and the remains of an
aqueduct which runs straight towards the pillar. The 'Iron-man' also
shows very little sign of rust, and its actual origin is unknown.
Although the origin of this pillar is unknown, the technique and
the style point to a date of manufacture in the late Middle
Ages. (4)
(Prehistoric
Germany)
Other Eigmatic Metal Discoveries:
1968 -
Semi-ovoid metallic
tubes of identical
shape but varying size found in Cretaceous chalk. The chalk-bed was exposed
in a quarry at St. Jean de Livet, France, and is estimated to be at least 65
million years old.
(3)
Mechanically manufactured gold thread
found in sandstone rock, Rutherford-Mills, England. It was found embedded in
naked rock, at a depth of about 8 feet. 60m yrs. (The Times, June 22nd 1844)
(8).
1881
- An 'iron nail'
from gold bearing quartzite from Kingoodie, Nr Dundee, 387m yrs. (The Times,
Dec 1881).
1891 -
Morrisonville, Illinois, USA. An 8 carrot (alloy), gold chain found
embedded in coal by Mrs S. W. Culp. As she undertook to take the chain from
the coal, the middle of the chain became loosened while each end remained
fastened. (estimated at 260-232 million years old).
(9).
1942
- Iron chain
still embedded in sandstone, California. Extant photo but object lost.
(Other Examples of Oopart's)
Copper
Mining
in Rudna Glava, Serbia (Vinca Culture):
The early Neolithic
Vinca mine of Rudna Glava near Majdanpek (5,000 B.C.) is an
example of the oldest known technology of copper working. The developed
skills of the Rudna Glava miners are indicated by the ore-emptied shafts no less than 20m deep.
Stone mallets, made from river stones
of volcanic rock, gives evidence of the higher
specialization of primitive tools for different and
various productive purposes. As for the chopping of the pieces
different types of wedges were used, while the tools made from
deer horns were used for gathering the ore already chopped.
When an ore vein was
discovered, the access platform was built round its flooding
canal. Afterwards the hard ore mass was broken into pieces by
circular hits with stone mallets, hanged either on a rope or leather
belt. In the depths, the technique of heating then cooling
suddenly was
used. Large ceramic dishes were used for
pouring the water over the hot ore blocks. Cracked blocks were
further smashed and broken into pieces.
The ore obtained was
taken to the surface in bags, and it was distributed to
the settlements near by. Further metallurgic processes are
considered to be a part of technological circle of handworks in
that early period of metal usage.
-
(Full Article:
http://www.muzej-mpek.org.yu/e_rglava.htm)
-
-
Mining for copper in Wales: (Extract...)
In July 1993, a Research Steering
Committee was set up to co-ordinate research on the Great Orme,
North Wales, a precipitous headland rising 220 metres above the
Irish Sea. The extensive copper mineralization hosted by this
isolated outcrop of Carboniferous limestone was exploited in
prehistory.
In their search for copper, the
prehistoric miners produced a labyrinthine complex of rifts and
galleries within the headland, which date primarily to the Bronze
Age (the second millennium BC) and cover an area of at least 240
metres by 130 metres, with vertical depths of up to 70m (Lewis
1997: 106, 158). The extent and unparalleled degree of
preservation of these workings render the Great Orme copper mine
one of the most important sites in Britain and Europe for research
into prehistoric copper metal production.
(Article:
http://www.assemblage.group.shef.ac.uk/4/4wager.html )
Mining in Ancient Britain:
(Extract...)
For more than half
a century archaeologists have grappled with the enigma of
Britain's first use of metals. It appears to have taken the art of
metallurgy more than 2,000 years to travel from the ancient Near
East and Balkans to Britain, and its dramatic arrival in about
2500 BC prompted early scholars to suggest direct contact between
Britain and the great metal-using civilisations of the
Mediterranean. The images evoked were of roaming metal prospectors
searching savage lands for raw materials. The reality may be more
prosaic, but is no less interesting.
In fact, the long
history of metallurgy was not just a Mediterranean affair. For its
origins we have to look several thousand years before the Castell
Coch artefacts were deposited in their shallow sanctuary. The very
earliest copper objects come from settlements and graves of the
late 8th/early 7th millennium BC in Mesopotamia and Anatolia, and
these are thought to be the products of rare outcrops of copper
metal (not copper ore) found in some parts of this copper-rich
area.
The momentous
discovery of smelting came later, in the mid-5th millennium,
seemingly independently in Anatolia, Mesopotamia and the Balkans.
By this time copper miners were hard at work at places such as
Aibunar in Bulgaria and Rudna Glava in Serbia, where rich veins of
copper oxide and carbonate minerals were being emptied to make
what must have seemed an entirely new kind of material. Hard
enough to sharpen to a cutting edge, yet tough enough not to
shatter. Infinitely re-meltable and re-useable.
After perhaps a
thousand years of Balkan copper production, the deposition of
copper in hoards and graves faded away. The technology was not
lost though. As dramatically as it appeared to decline, metallurgy
was back, but this time in a different location and with a new
sort of metal. In the mid-4th millennium, arsenical copper was now
taking centre stage with a new focus on Alpine and sub-Alpine
Europe. A similar copper-arsenic alloy was developed in the old
copper-producing centres of the Near East, although there the
transition took place without the production hiatus apparently
experienced in Europe.
Exploitation of the
rich Alpine copper required the development of a new technology.
Unlike the Balkan ores, the Alpine deposits were mostly of copper
sulphide minerals. Unusable as mined, these had to be roasted
before smelting to convert the sulphide minerals to the oxides
that would have been familiar to the Balkan smelters. In practice,
lumps of sulphide ore were placed on a hot wood fire and stirred
round, to introduce plenty of oxygen and convert the ore to copper
oxide. The oxide ore was then smelted in an enclosed furnace
heated by charcoal with as little oxygen as possible to reduce the
ore to metal. Such roasting beds and smelting furnaces dating from
the later Bronze Age have been found in the Mitterberg region
south of Salzburg.
Recent research
suggests that early metal workers knew exactly what they were
doing in using these ores. A significant addition of arsenic to
copper produces better mechanical properties, and higher levels
produce a metal of striking silvery appearance. Artefacts with
higher levels tended to be `high status' objects such as knives
and daggers, while everyday tools, such as the 4th millennium BC
Iceman's axe, contained less. The proportion of arsenic in
artefacts ranges from less than 1 to 7 per cent - never more than
that - while ores can contain up to 30 per cent, suggesting that
arsenic quantities were being controlled.
The evidence for
such mixing comes from slightly later periods, but might apply
equally to the 4th millennium. At the mine site at Ross Island in
Ireland, for example, dating from the mid-3rd millennium, the ores
are varied, containing anything from a few to about 30 per cent
arsenic. However, the metal produced was much more consistent,
suggesting that the ores were mixed. Later still, in the 2nd
millennium, the Great Orme mines in North Wales produced perhaps
hundreds of tonnes of copper at a time when most artefacts
contained some degree of arsenic, and yet the Great Orme ores
contained no arsenic whatsoever. The Great Orme metal was clearly
not used without some degree of adaptation.
Whatever the truth
of central Europe's arsenical copper in the 4th millennium,
Britain remained literally in the Stone Age. It would be a
thousand years before the island periphery of north-western Europe
was to experience metallurgy at all. And yet when it came, the
metals revolution took off with explosive technological pace.
Within a few hundred years not only was a Continental-style
arsenical copper industry thriving here, but by about 2000 BC the
harder, tougher alloy of copper and tin known as bronze had also
been invented. It replaced arsenical copper across Europe and
dominated the European metals scene until the coming of iron more
than 1,000 years later.
It is perhaps not
strictly true to say that bronze was invented in Britain. The very
earliest combination of tin and copper is found in Anatolia, but
Near Eastern bronze contained less tin, in less standardised
quantities, than was found in British bronze. Put simply, it was
inferior bronze. In Britain, bronze was produced from the outset
with an almost standard composition of 8 to 12 per cent tin,
ensuring the optimum mix of qualities. For archaeologists the
rapid establishment and spectacular success of metallurgy in the
British Early Bronze Age, from 2500-2000 BC, is something of a
quandary. How did metallurgy arrive in an apparently advanced
state? Who brought it and why did it take off here so well?
In fact, the region
where early tools and weapons suddenly appear in large numbers is
south-west Ireland, predominantly in the form of simple `flat'
axes. Wherever it was made and traded, more of it was left behind
in the rugged Atlantic coastal landscape of Munster than anywhere
else. This Irish metal was not inferior stuff either. What was
being made and deposited was not the simple copper of the earliest
European metallurgy, but arsenical copper, the superior material
pioneered in Alpine Europe and, by this time, also commonplace
throughout the Mediterranean as far west as Spain and Portugal.
So how did this
advanced technology suddenly come to Ireland, and why? Who were
these metal makers? To a previous generation of archaeologists
such developments could only be explained by the invasion and
settlement of new, technologically advanced, people. If not Greeks
prospecting for precious ores, perhaps Iberian settlers made their
way north along the Atlantic coast seeking out sources of the
arsenic-bearing copper ores with which they were familiar.
This notion of a
mass movement of people, even an invasion, found support elsewhere
in the archaeological record. The arrival of metallurgy was not
the only big change taking place in the middle of the 3rd
millennium, but the period also saw the appearance of beaker
pottery in the British Isles. These highly distinctive vessels,
often buried with the dead, were widespread in central Europe and
Iberia before they were used in Ireland. Was there a link?
(Article:
http://www.britarch.ac.uk/BA/ba56/ba56feat.html )
Egyptian copper mining:
(Extract...) Copper was the first metal to see
extensive use in Egypt. Copper tools, weapons, and ornaments are
found beginning approximately 4000 BCE. Conditions for miners were
described as �wretched,� and for most of the years of Egyptian
history, the work seems to have been done by teams of slaves.
Smelting to extract metal from the ore was almost
always done on-site, no matter what was being mined. Copper ore
was extracted and broken into small pieces and mixed with charcoal
fuel in a fire on the ground or in a shallow pit. This method
produced temperatures of between 700 and 800 degrees Celsius,
enough to separate the metal from the rock, but not hot enough to
reduce it to a truly molten state.
Estimates made from slag heaps
found at these copper mining operations indicate that an average
of five tons of copper were produced annually in Egypt during the
Bronze Age, which was not enough to supply the kingdom with its
metal needs, necessitating importation of copper as well as tin
for Egypt's bronze production. This harder, easier to cast metal
eclipsed copper as the major material for tools in Egypt after its
introduction from western Asia.
Egypt's history as a metal-using
culture extends deep into the past. Copper and gold tools and
ornaments date back to the Pre-Dynastic period and its craftsmen
have produced a myriad of beautiful treasures and practical tools
during Egypt's time as a power and a living culture. Although
Egypt was not the originator of metalworking, the exploitation of
the mineral resources under its control assisted in its rise to
power and craftsmanship.
(Article:
http://www.mnsu.edu/emuseum/prehistory/egypt/dailylife/mining.htm
)
|